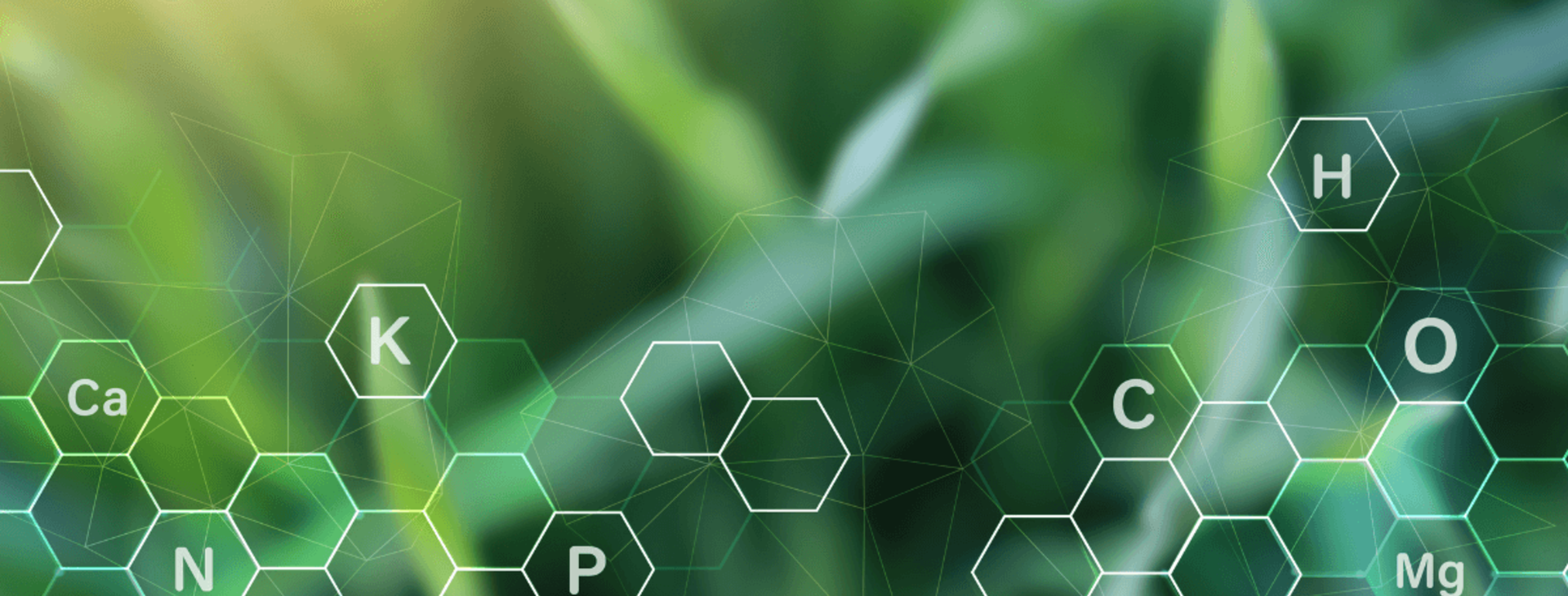
Our sustainability journey in pharmaceutical packaging
An interview with sustainability expert Agnieszka van Batavia
At Constantia Flexibles, we focus on innovation in sustainability and pharmaceuticals. To delve deeper into our sustainability initiatives and their impact on the pharmaceutical industry, we spoke with our expert Agnieszka van Batavia, Sustainability Manager Pharma Division.
Can you outline the key sustainability initiatives currently in place at our company, particularly those most relevant to the pharma industry?
Last year, we increased the level of our climate ambition and added a commitment to setting a SBTi approved Net Zero target on top of the already SBTi approved absolute scope 1-2-3 GHG emission target. This means that right now, all hands are on deck to ensure we can achieve this challenging goal, from purchasing raw materials to finding a solution for green heat generation. All of those initiatives lead to the reduction of the carbon footprint of our product, which directly translates into scope 3 reduction for our customers.
What are the latest developments in sustainable materials for pharmaceutical packaging, and how is our company leveraging these innovations?
In the world of perfect barriers, there is no better solution than aluminum. This lightweight metal is infinitely recyclable but is also known to have a relatively high carbon footprint. Up until now. With the introduction of low carbon aluminum, we have revolutionized the high-barrier blisters portfolio by offering a 30% reduction in carbon footprint without any trade-offs. Because the alloy composition remains the same, there is no change to the specification of the final packaging material. There is no need for time-consuming stability testing and no need for costly revisions of the drug master file. Another hot topic in pharma packaging is moving out of PVC in both cold forming foils and thermoform blister systems. Constantia Flexibles is answering those needs with an innovative portfolio of alternative blister pack solutions: From Regula Circ – our PVC-free cold forming foil, to FUNDA – a PVC-free base for a thermoformed blister.
In the world of perfect barriers, there is no better solution than aluminum. Low carbon aluminum has revolutionized our high-barrier blisters portfolio, offering a 30% reduction in carbon footprint with no trade-offs.
How do sustainability efforts intersect with regulatory compliance?
Regulatory requirements and sustainability in pharma packaging go hand in hand. Both require us to apply science to minimize the negative impact on people and the planet while maintaining packaging function that is vital for ensuring safe medicine delivery and patient well-being.
Please explain our approach to packaging lifecycle assessment and how it influences our sustainability practices.
Life cycle assessment (LCA) is a scientific methodology for identifying and quantifying all materials, energy, waste, and emissions involved in the lifecycle of a product or service and calculating their impact on the environment. It allows us to focus on hot spots in the product life cycle where the highest impacts occur so that we can design targeted strategies to reduce those impacts. Our LCA studies typically cover the so-called cradle-to-gate scope, representing our activities, excluding packaging and transport to the customer and including production of energy, raw materials, and ancillary materials, manufacturing of the product, and upstream transport routes. All data associated with conversion processes at Constantia Flexibles are primary data collected at specific sites. We combine those inputs with consistent background data from internationally recognized LCA databases to ensure an accurate result.
Are there any collaborations with other industries or academic institutions helping to drive innovation in sustainable pharmaceutical packaging?
The pharmaceutical industry is driven by science. At Constantia Flexibles, we recognize that having access to the latest scientific research is important. That is why we applied for membership in IAPRI – the International Association of Packaging Research Institutes. Being part of this platform facilitates the exchange between different academic institutions and our technical organization.
What are the biggest challenges and opportunities you see in achieving sustainability in pharmaceutical packaging?
Achieving circularity in pharma packaging is, in my opinion, the biggest challenge we have. Even if pharmaceutical packaging has been designed for recycling, in most cases, it will not be recycled in practice because it is not allowed in the general packaging recycling stream due to contamination with medicine residue. The only exception here is the PVC-free aluminum cold forming blister, because of how the recycling process of aluminum works. During the smelting of aluminum waste, all polymers and potential medicine residues are incinerated, and what is left is metal that can be used in new applications. When it comes to opportunities, moving away from PVC is one to consider. Replacing PVC with polyolefin-based alternatives results in a reduction in the amount of plastic used in packaging, also leading to a potential reduction in greenhouse gas emissions. Our commitment to sustainability and innovation in pharmaceutical packaging showcases our dedication to environmental stewardship and meeting the industry's evolving needs. As we continue to forge ahead, our initiatives promise a greener and more sustainable future for pharmaceutical packaging.